From the 24th to the 26th of October 2023, the 9th edition of the European Lean Educators Conference took place. Three days filled with ~100 people with a shared passion to educate others in Lean. Our colleagues, Product and Process Specialists, ánd Black Belts Martijn Buijvoets and Theo de Goede went to the Conference. In this article, Martijn shares the lessons he took home from the keynotes he attended.
Disclaimer: This article reflects the personal notes and memory of the author. It has not been peer-reviewed and may contain flawed recollections of the intentions of the speakers.
DAY 1 - TUESDAY 24 OCTOBER
The program started in the afternoon with a great kick-off by Prof. Jaap van den Heuvel. He provided the first keynote where he shared about his journey of initially using Six Sigma as main improvement method, up until 2013 where he got exposed to Lean. His key message was: Lean and Six Sigma are very powerful methodologies that can turn the tide in Healthcare to enhance quality while lowering the costs of Healthcare delivery. Surprising therefore that they are only implemented in a limited number of hospitals.
For me it was quite interesting to see Six Sigma and LEAN method positioned individually. I was taught these methods interchangeably as "Lean Six Sigma" and have been using those teachings as my go-to structured improvement methodologies. Therefore it is difficult for me to grasp that not combining the Lean foundations and Six Sigma breakthroughs is common (at least in The Netherlands).
Later in the afternoon, Dennis Gawlik's contribution contained a lot of golden nuggets for me:
- 76% of Lean teachings are about Lean tools (and only 13% of Lean teachings include systems thinking)
- After Womack and Jones published their book in 1996, we often stop with the book and tools and don't dig further into the philosophy and principles behind Lean. We don't collectively teach the basics of Deming, Ohno, and others that laid the foundations.
- The difference between Continuous Improvement and Continual Improvement is a subtle one related to the intensity. Continuous improvement is a siloed focused improvement, while Continual improvement takes combined working and stopping to reassess if this improvement needs further work or if efforts are more worthwhile in other improvement areas.
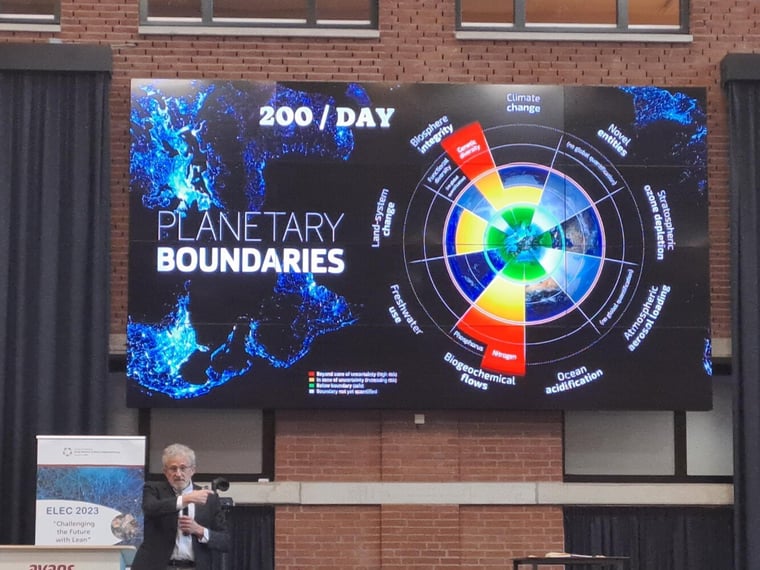
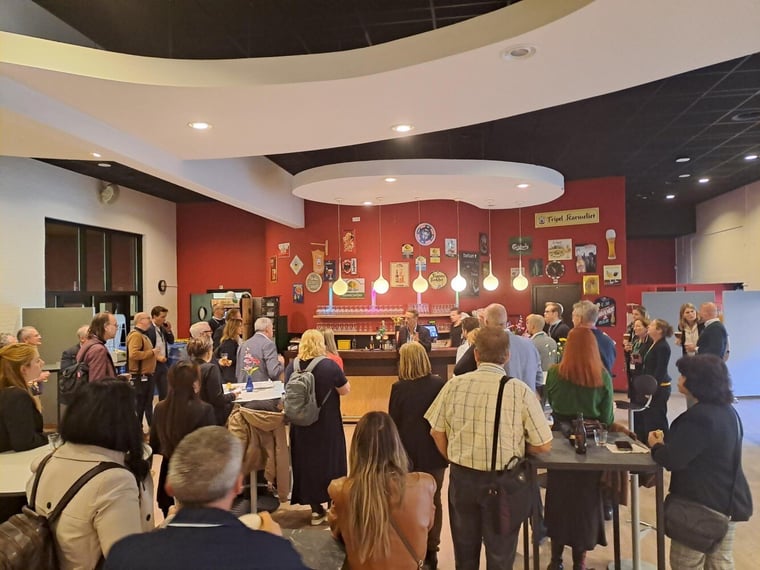
DAY 2 - TUESDAY 25 OCTOBER
#ELEC2023 Day 2 was filled with amazing content and ended at a very special diner location in the Jheronimus Bosch Art Center. Here are my nuggets.
Komberianov Serhii started the day with a keynote that gave me goosebumps: How Lean practices can help in a war crisis. The Ukrainian economy was shocked by the war, 57% of businesses ceased their operations. Serhii covered 3 major challenges in his talk.
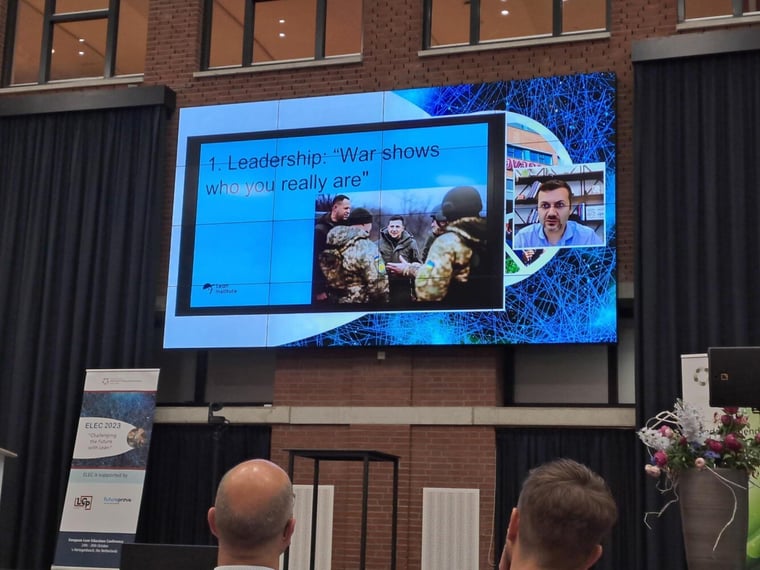
1. LEADERSHIP STRUGGLES TO ADJUST TO THE NEW REALITY
At the start of the war, nobody was prepared. From one day to another there was an overload of tasks that were critical for the survival of a business, and structured problem-solving did not get priority. Where leadership decisions pre-war generically focused on reputation and immediate action/fixes for problems, leaders now have to think more long term and were reminded that focusing on people in an authentic manner is actually critical for economic survival and supporting the country. Companies that survived the first 6 months came back stronger. This reminded me a lot about the Worse-Before-Better behavior that I studied for my master's thesis (described e.g. by John Lyneis and John Sterman in their 2016 article on Capability Traps and the Failure of Win-Win Investments in Sustainability and Social Responsibility). His last important lesson on this topic was to set small goals/targets/tasks for employees to achieve small victories every day. This is important for building a culture and staying optimistic.
2. OPERATIONS HAD TO BE RELOCATED TO SAFER TERRITORIES
Organizations that were already advanced in Lean practices (e.g. low inventory / work-in-progress) were able to move more easily. Also, companies that were structured over processes instead of functions were more mobile as well. At the same time, the new premises were structured in such a way that they were more modular and transparent, flexible with an open layout.
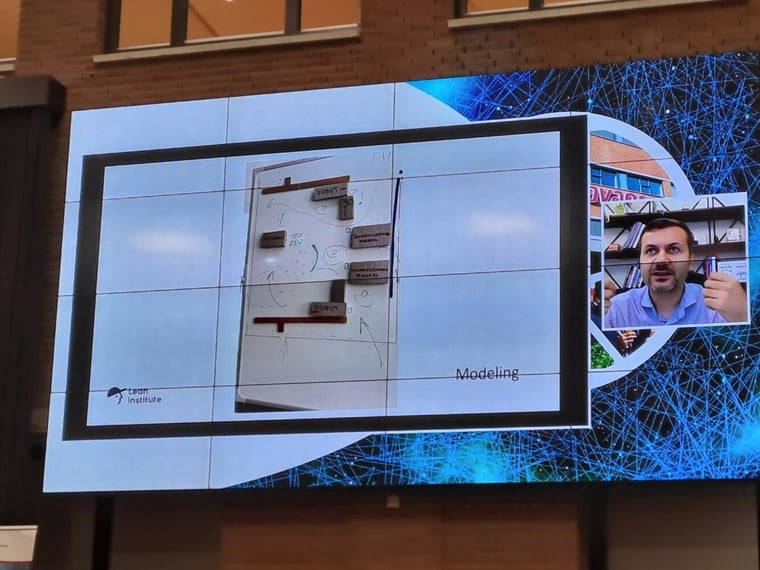
3. LOSS OF EXPERIENCED PEOPLE (20% JOINED THE ARMY, 30% FLED THE COUNTRY)
This caused a dire need for rapid development of capabilities. Training Within Industry proved to be a key driver of quickly increasing the skills of labor forces, using a skill matrix is super effective. Interestingly, implementation of methodologies like TPM became easier since employees felt incentivised to help the country survive economically. This led to a better understanding of being trained more broadly since at any moment a colleague could go to war.
Many thanks, Serhii for sharing these extremely valuable lessons!
Joriene Beks followed up. She had the challenge of transitioning the crowd from a threat to physical safety to how to design psychological safety in a work environment which was done wonderfully. We are all human, that is our common denominator. Working in a psychologically safe environment is a critical success factor for high-performing teams. While fear may work better in the short term, it won't have a lasting benefit.
Parallel Session on Education
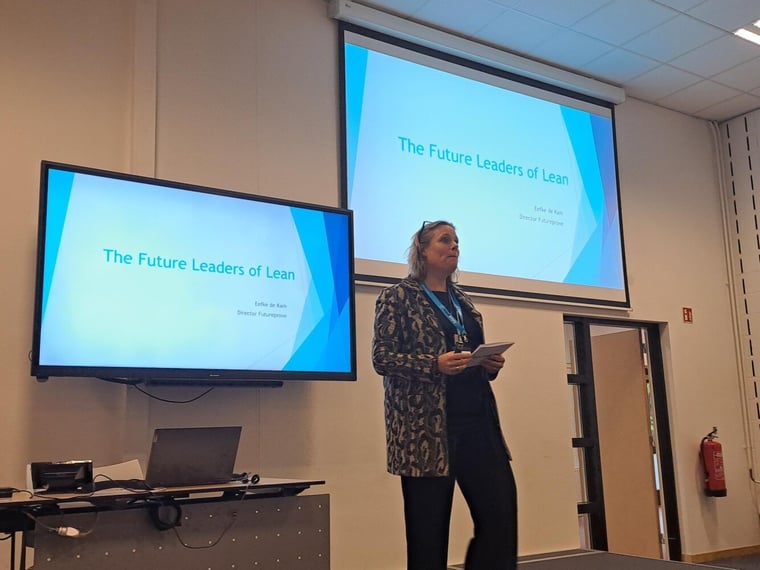
In the Education track, Eefke de Kam had a parallel session on the future leaders of lean where she talked about the model behind her company Futureprove where trainees complete 4 LSS projects in 2 years. Future leaders have to be adaptive and know what others need. Her company matches Lean Six Sigma talents to companies (like other recruitment and consultancy firms), she provides a customized education path and mentoring to young trainees.
She shared her lessons about GenZ: they are perfect as they are, they work to enjoy life (4d/week should be enough), they want to exceed expectations and are ambitious, and they want to make their own choices (you can't control how someone develops). Finding the balance in each person's path is a challenge. Mentoring helps a lot with this by e.g. helping to choose the right tool for the right intervention at the right time. Trainees are hired for attitude, LSS you can train. Students also get confidence from the Black Belt (of which 50% of the tools they don't use anymore). She ended with the quote: "if it is up to be, it is up to me" which inspires her and the trainees.
Eefke wrote a blog in which she reflects upon her talk, highly recommended (in Dutch) https://futureprove.com/inspiratie/the-future-of-lean-leadership/
"GenZ is perfect as they are. They work to enjoy life, they want to exceed expectations and are ambitious. They want to make their own choices. Finding the balance in each person's path is a challenge."
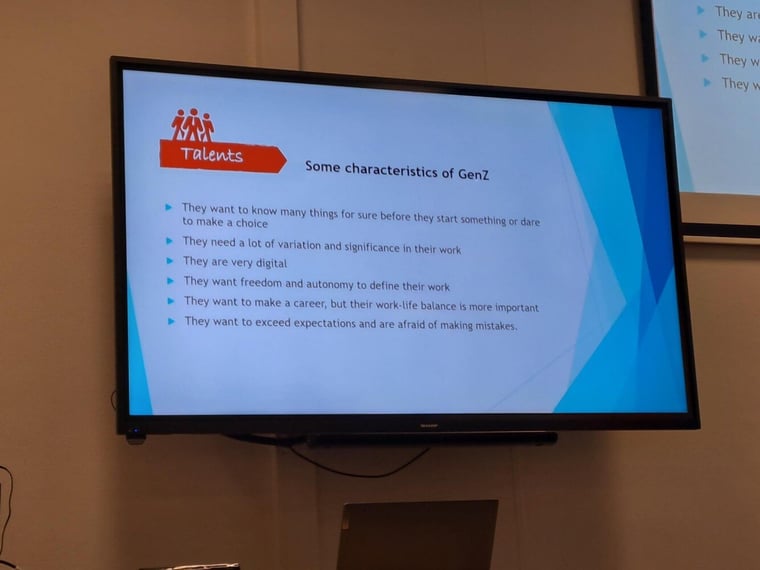
Jesse Reuken followed up Eefke, who is about to finish his traineeship at Futureprove, and shared his lessons learned from the four LSS projects he completed. A few nuggets I picked up:
- Decision makers on the implementation of improvement project solutions can be different people than those who sponsor your improvement project, you have to navigate all stakeholders.
- Focus on what you should monitor, not on what you can monitor.
- Letting go of control and "being okay" that you don't fully understand a topic is sometimes needed to meet the deadline (in the context of ASML a highly complex Dutch business)
- Just doing often gets you far.
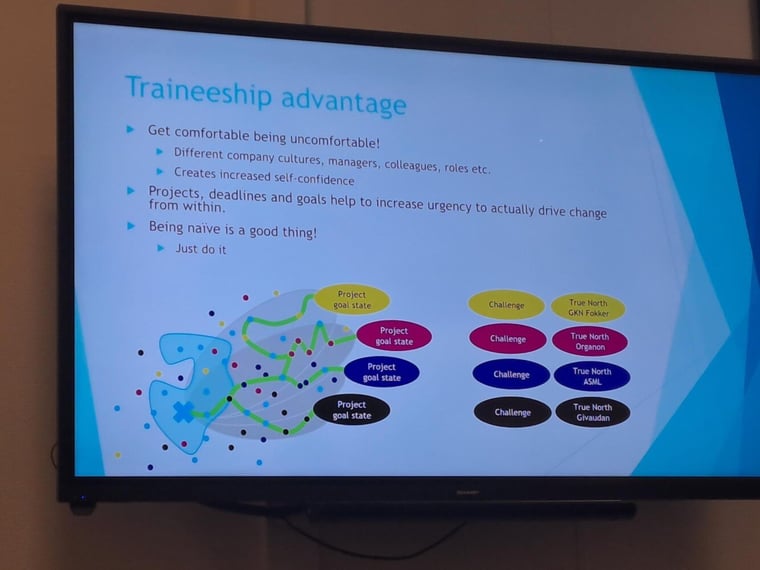
Stephanie Monfils shared her research on how Lean-themed internships can be more successful. She highlighted the case study where Avans Hogeschool is collaborating with Amphia in Breda. In 4 years the "Care Simplifiers" (Dutch: Zorgversimpelaars) program has delivered ~40 successful projects for the hospital and educational Lean Green Belt experiences in practice for students.
Afternoon Keynotes
Dr. Michael Sanders got us all awake during the afternoon when he rapidly fired thought-provoking facts in his talk on Quantum Lean! Value is the difference between benefit and burden. Time however is natural, and often the most critical element.
Quantum Lean is a product-centric approach to how inputs can be transformed into outputs. The Wisdom from the old masters like Deming and Ohno was all in the context of products. To rightfully apply the methods we know nowadays, we should be aware of the original source context and the meaning of the method within that context. If we don't fully comprehend the true meaning - "we do not deserve to use the methodology and should get the vocabulary out of our system". This comment reminded me how easily the sources of the methods we use nowadays are lost through a widespread focus on the usage of the tools themselves.
As further reading he brought copies of his book and recommended us to read the ASQ paper Timing Is Everything.
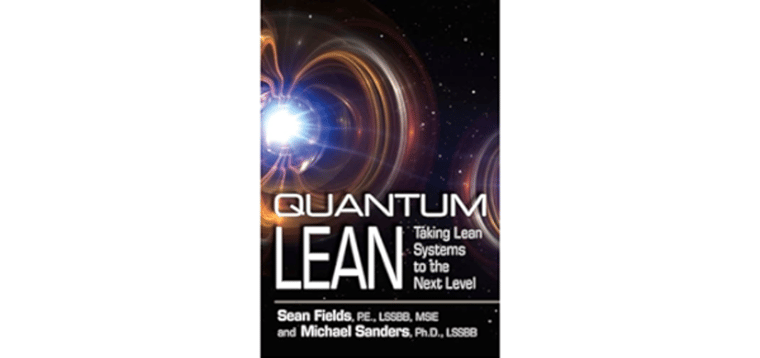
Dr. Michael Sanders shared copies of his book with the audience after his keynote. I look forward to reading the book.
Up next was Mark Hijmans from ASML, the title of his keynote said it all: 'Change comes from within.' He started by explaining that you should Think, Feel and Do. He especially highlighted that it was important to create high-impact confrontations with a special focus on actually going to the work floor and seeing and feeling for yourself. Organizations will only start moving when they are aware, therefore ensuring people see the same goal and deliver valuable rewards for them to incentivise movement for the required change. Another nugget for me was that you can't program cultural change.
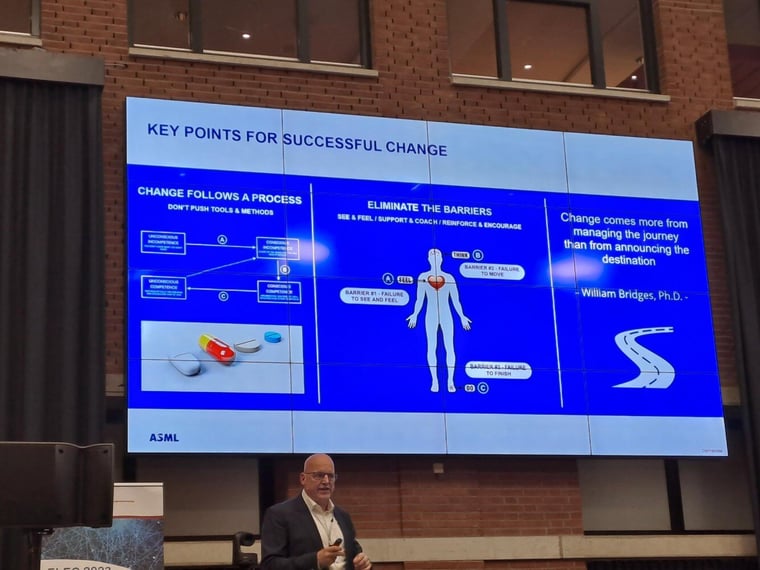
Mark ended by sharing the challenges between the strong Technological leadership position ASML must have to keep up with societal demand, but at the same time in his role, he is challenged by trying to have the Operational Excellence keep up with the fast-paced technological developments.
After a long day filled with new insights, we all had a relaxing dinner in the truly inspiring Jheronimus Bosch Art Center.
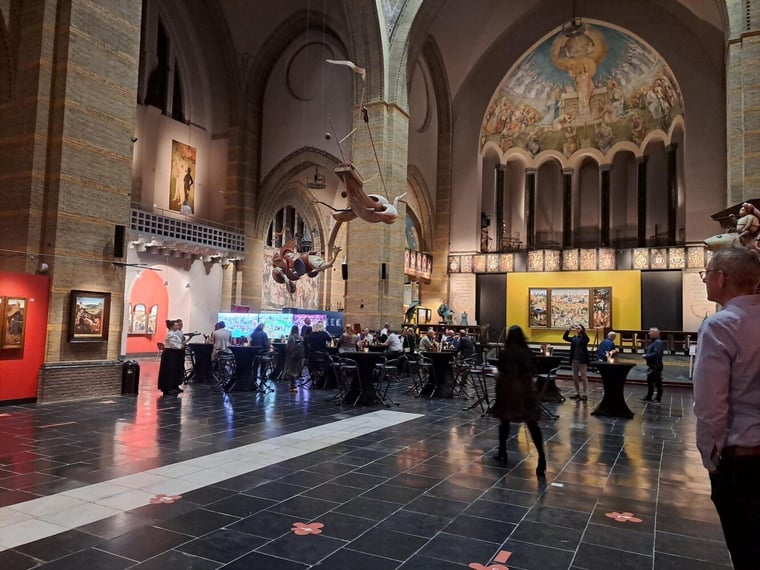
DAY 3 - THURSDAY 26 OCTOBER
The last conference day continued with a joint keynote of Jim Lippens and Iris Hond.
Joint Keynote -Jim Lippens
Jim started his part with a concerning statistic: only 13% of the Dutch workforce is engaged in the Netherlands, and employee engagement in Europe is lowest compared to all other geographies surveyed (source: gallup study). He related this to the under-utilization of human potential in organizations (also known as the 8th waste) and suggested the use of the Harada Method.
The Harada method helps people to become self-reliant. Self-reliance is not a goal in itself, but a methodology and a mindset in which every goal is attainable. It's about finding guidance from within, being independent, confident, and conscious about yourself. When people know how to take full responsibility for their own lives, they can focus on personal success, well-being, and happiness and thus better serve the organization they work for (and the society in which they live). It was created by Takashi Harada and written down by Harada and Norman Bodek, both good acquaintances of Jim.
Jim also presented his 4D Lean framework:
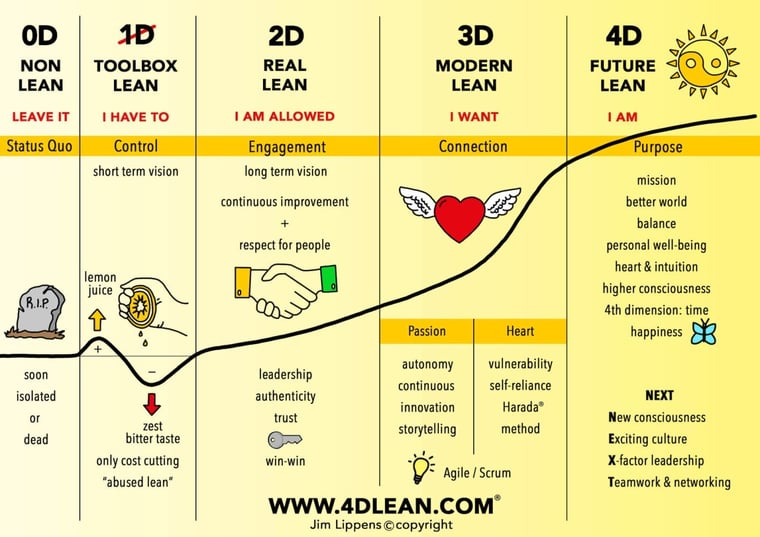
I understand his model as a maturity framework of how organizations apply Lean.
- 0D -> Organizations are satisfied with the status quo and will soon be obsolete. LEAVE IT as it is, is the default response of employees.
- 1D -> Organizations focus on Control have a short-term vision and focus on cost cutting. Toolbox of lean is dominant and there is a culture of I HAVE TO. A people manager is needed to get organizations out of 1D.
- 2D -> Trust within the organization is the biggest difference, leaders are authentic, there is a long-term vision, and employees are engaged and feel allowed to own their work.
- 3D -> Organizations seek out the passions of individuals and leaders and employees alike dare to be vulnerable to give it all they got. Step-function innovation is possible (continuous innovation compared to continuous in 2D). The Harada method is used to let employees be self-reliant. There is a strong focus on connection based on "Humanness".
- 4D ->Organizations have a clear mission and want to contribute to a better world. Balance, personal well-being, feeling, and intuition are basic elements in an environment that strives for happiness for everyone.
An ideal future-proof organization has a good mix of 2D, 3D, 3D+, and 4D. You can do a self-scan on Jim's website: 4D Lean Scan.
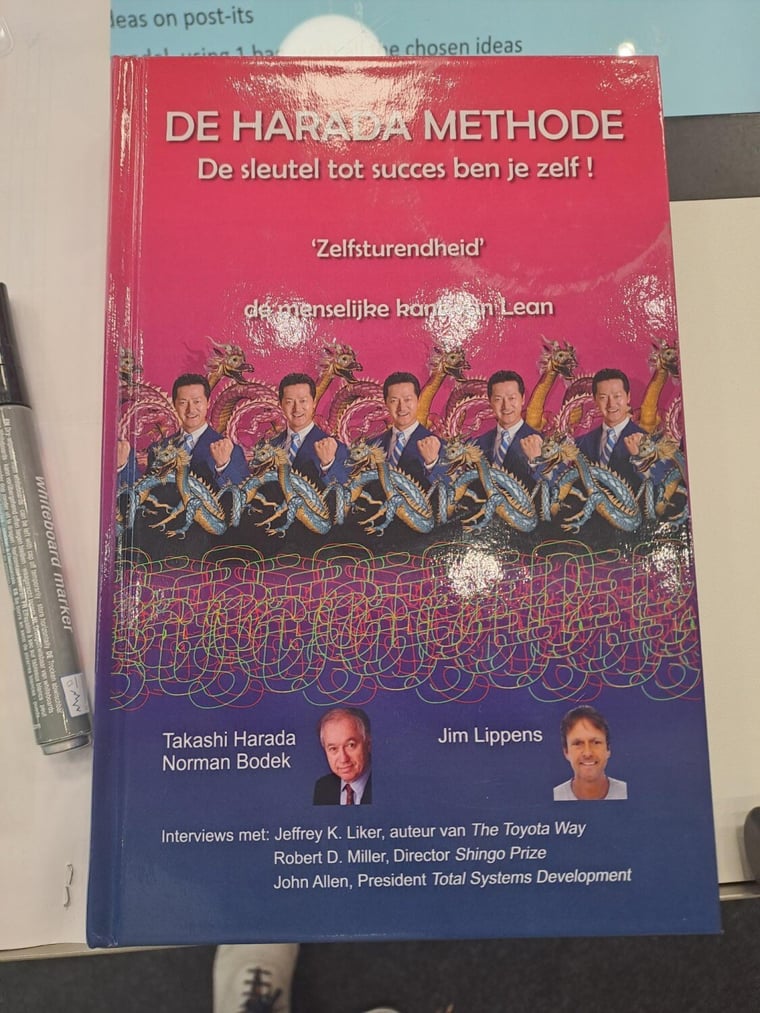
Jim finished his part of the keynote with a story on how he organized the Happiness@Work - Conference 2022 for which he worked 10.000 hours to deliver a message of inspiration to CEO's and HR workers. Just one day before the conference everything was prepared and he allowed himself a moment of rest. In this moment Iris played a few notes on the piano and those notes were his reward for the hard work he'd been putting in. In those few seconds, Jim felt like he was 'being'. This feeling was the common denominator between the joint keynote of Jim and Iris: explaining and exhibiting the power of vulnerability and connection - the biggest jump from 3D to 3D+ in the 4D model.
After Jim shared his vulnerable moment about Iris' notes, she started playing very softly on the piano...
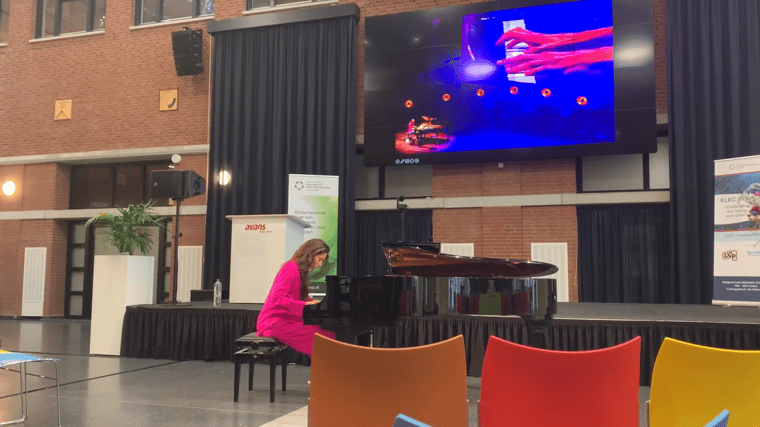
Joint Keynote - Iris Hond
When Iris was done playing, she stood up and opened her part of the keynote with the sentence: "Everyone has a story."
Through sharing her personal story Iris showed how being vulnerable has helped her grow. When you lean into your emotions, they can be turned into something beautiful. While growing up it felt safer to keep up an appearance than facing it. Only when she lost control of her emotions when she was at a very low point, did the tide start to turn and she felt ground under her feet again, she felt seen and heard, and someone felt for her.
Making a deep connection through vulnerability is very powerful. While the conservatory taught her how to play the piano, through her life experiences she truly experienced the power of music. You can't prepare for life, step out of your comfort zone and go live.
Before playing closing music on the piano, Iris closed off with some powerful lessons:
- We are all equal. Respect is the starting point
- Create a culture of belonging. Being genuine is important for CEO's and assistants alike
- Make a real connection. Show yourself, dare to be vulnerable
- Don’t judge … everybody has a story
Snippets from the joint Q&A:
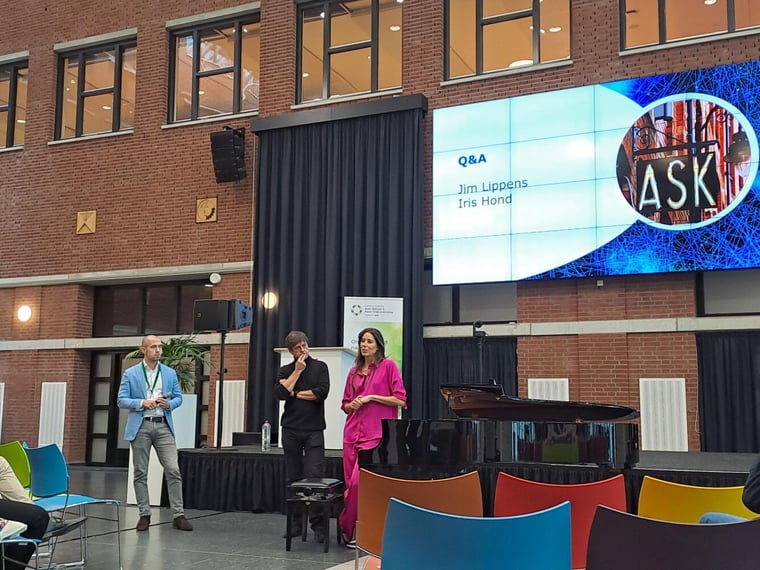
Q: Why don't we want more connection? A-Iris: There is less and less connection, Technology disconnects parents and children through phone usage.
"The Truth is in the heart"
When sharing, keep it small land true to yourself. After you start to share you feel strong.
"There is always a connection between humanness."
Last keynote of the conference
Rose Heathcote's keynote was about 8 ways to improve the world. She first challenged the audience to think What does Sustainability mean to you? There are different definitions in circulation and this doesn't make it easier to understand sustainability in day-to-day life - Sustainability is a big word. The Sustainability definition she recommended was: "Meet the needs of all, in the context of the planet." Another definition Dennis Gawlik later shared with me that I also liked is: "Sustainability is the possibility that humans and all life will flourish on Earth forever."
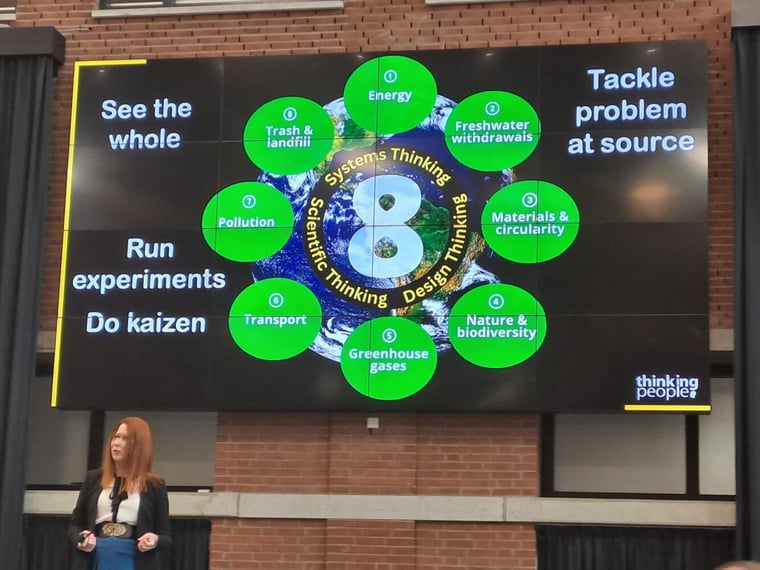
We need to revise how to collaborate
- Ban single-use anything
- Reduce long distances in supply chains
- When you save inputs in the product design (make it more lean), you improve the sustainability of the product lifecycle as a whole
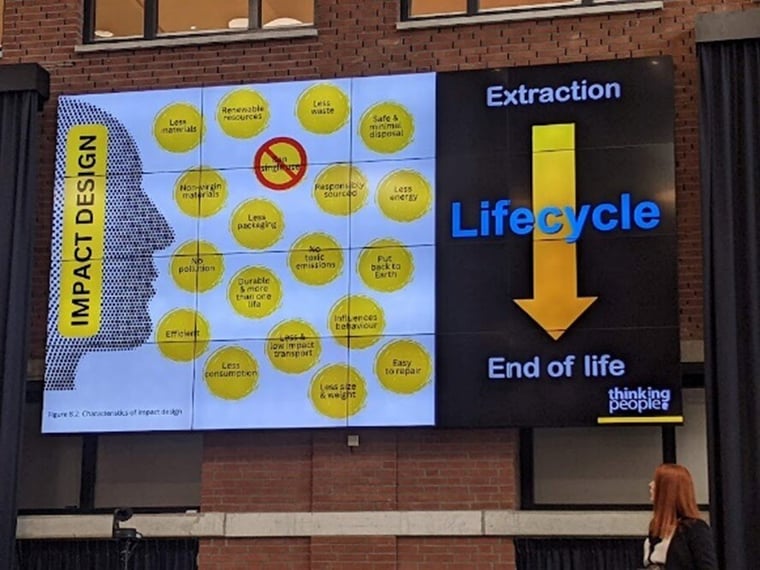
Conclusions
ELEC2023 was a conference that lived up to its title: Challenging the Future with Lean. Many impressive speakers shared even more lessons with the audience.
Personal highlights for me were Dennis Gawlik's reflection upon the current state of Lean (Six Sigma) methods, Komberianov Serhii's shared experiences how Lean efforts increase effectiveness during a crisis, Eefke de Kam's sharing the secrets behind the success of Futureprove, and I was most impressed by how Jim Lippens and Iris Hond served the audience with a joint experience instead of 'a keynote' and highlighted not only rational but also the emotional aspects of how humans can utilize Lean.
Here are my 5 take-home lessons, wrapping up 3 packed days of conference (with references to keynotes):
- Lean is a people business. The mechanics and tools are nice and cool, but true change happens in the hearts and souls of people (Iris Hond). In my experience, we often forget to fully incorporate the human connection in lean implementations. Therefore we miss out on the Respect for People pillar and put too much emphasis on the mechanics of Lean. We have to ensure that the people we work with feel safe first (Joriene Beks) and we have to think, feel, and do (Mark Hijmans). Utilizing the 4D Lean framework and making people self-reliant via the Harada method will help to obtain the human connection again and let organizations flourish (Jim Lippens).
- Systems thinking should be utilized more to obtain bigger benefits from Lean methods (Dennis Gawlik & Rose Heathcote). Perhaps we can start modeling the big societal challenges as a set of inter-related Capability Traps (inventor John Sterman explaining the basic model in video 0:49-5:00). Only when we can put shared efforts behind a common goal, lean methods have the potential to flourish and are highly effective (Komberianov Serhii).
- The future leaders of Lean will need all the support and guidance to collectively tackle the big societal challenges ahead - especially in making the world a more sustainable place. We are all in this together. (Eefke de Kam, Dennis Gawlik, Rose Heathcote). Personal additions: I foresee a strong need in the future to spread effective problem-solving methods to a wider audience that can help tackle the grand challenges ahead. I'm proud to have contributed to the work of the ESTIEM Lean Six Sigma Green Belt course that is now able to teach 300 European students annually and follows the vision: Through developing our students during and after the course, we cause European-wide, measurable, and accumulating impact in the organizations they work. Here we specifically focus on the impact students make with the knowledge in real life and go beyond merely transferring knowledge.
- Focus with Lean on the product, that's where you will reach the most gains in speed (Dr. Michael Sanders) and sustainability (Rose Heathcote).
- A purist, but in my opinion valid take-away: We should fully comprehend the origin of the methodologies we use daily to apply them well (Dennis Gawlik and Dr. Michael Sanders). Personal additions: Seeking the insights the original inventors sought will help us to not create distracting deviations - as many anomalies over the methods have emerged over time due to misinterpretations/mistranslations/oversight/etc. As a field that preaches the saying of Taichii Ohno: "Without Standards, there can be no Improvement." we still have a long way to go to set universally accepted standards that reference the source.
Lastly, I'd like to express my gratitude to everyone who made this event so very special. Thanks to Ton van Kollenburg and his team from Avans Hogeschool for tightly organizing this wonderful gathering and accommodating all of our needs. Thanks to all the speakers that I mentioned above and those I didn't manage to include in this write-up. Thanks to my colleague Theo De Goede who was my companion during the event. I'm grateful to Holland Innovative, especially Marcel Logger for facilitating this opportunity. Finally, I'd like to be thankful to all the people that I talked to and connected with during the conference who enjoyed talking about improving the world together.
Lean is a people business, that's what makes it fun for me.
"We are Here to Have Fun, to Learn, and To Make a Difference" ~ Dr. Deming